Cargo tank inspections
Traditional and Drone-Assisted Cargo Tank Inspections
The standard cargo tank inspections will be carried out by our inspectors from the tank top as well as the steps. In the event that staging is unavailable, our inspector can be accompanied by a class-approved drone pilot in order to obtain a more precise assessment of higher spots or areas.
The use of drone technology allows us to capture more accurate and detailed images of the tank surface, providing a more precise assessment of the situation.
Scope of inspection:
The use of drone technology allows us to capture more accurate and detailed images of the tank surface, providing a more precise assessment of the situation.
Scope of inspection:
- Visual Inspection
- General view
- Pitting corrosion
- Cracks / Weld damages
- Passivity check
- Roughness check
- Ferroxyl Test
- Chemical Tests if required
- Report with pics / tank rating / advice.

Surface Condition Assessment
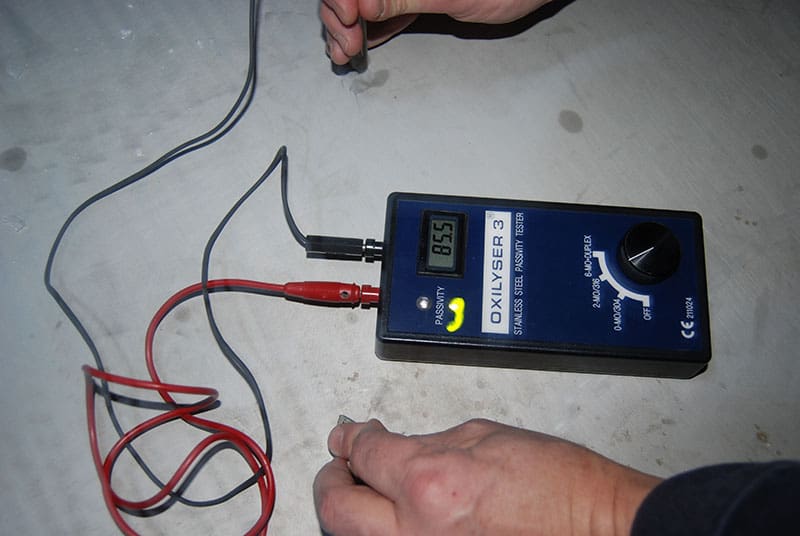
Passivity test
Measuring the Chromium Oxide Layer Thickness (which determines the real corrosion resistance and sensibility of the stainless steel surface).
Passive measurements show a surface resistant to corrosion.
Active values suggest a surface that is not resistant to corrosion, with a high potential for pitting corrosion or general corrosion.
Device: Electronic Oxilyser 3
Passive measurements show a surface resistant to corrosion.
Active values suggest a surface that is not resistant to corrosion, with a high potential for pitting corrosion or general corrosion.
Device: Electronic Oxilyser 3
Roughness test
Measuring the roughness or smoothness of the surface. High roughness will accumulate impurities in or on the surface, which might cause pitting corrosion. Because cargo residues will adhere more firmly to a surface with increased surface roughness, cleaning the cargo tank will take longer.
Device: Electronic Ra test device
For chemical tankers: Standard surface roughness for Clad Steel (a 3 mm stainless steel layer on mild steel) 0,5–2,0 Mu Standard surface roughness for solid stainless steel: 2,0–3,5 Mu
Device: Electronic Ra test device
For chemical tankers: Standard surface roughness for Clad Steel (a 3 mm stainless steel layer on mild steel) 0,5–2,0 Mu Standard surface roughness for solid stainless steel: 2,0–3,5 Mu
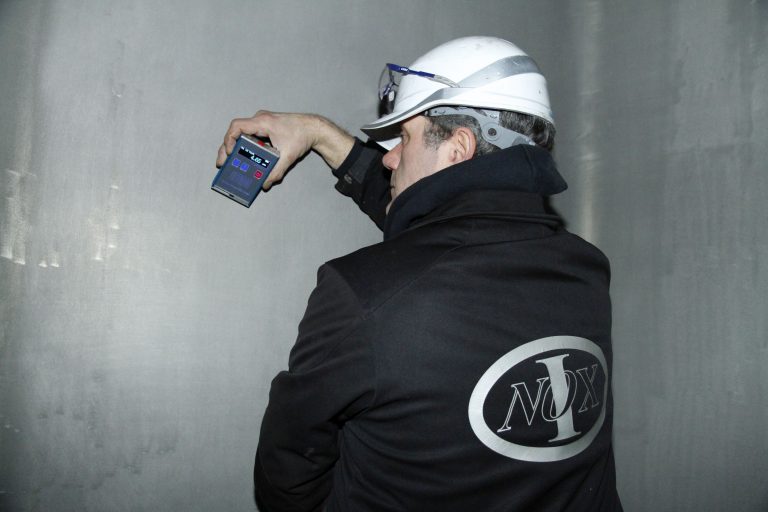

Ferroxyl / Blue Point test
On-site cargo tank inspections carry out chemical analysis to identify iron and steel residues on the surface of stainless steel.
By removing or reducing the passive layer in the affected area, these contaminants can cause pitting corrosion.
Device: Chemical solution and indicator paper.
By removing or reducing the passive layer in the affected area, these contaminants can cause pitting corrosion.
Device: Chemical solution and indicator paper.
Chemical test
To remove slight corrosion, discolorations, or cargo residue.
Mostly required when the tank will not pass cleanliness for the next cargo or to upgrade the tank’s surface condition.
Mostly required when the tank will not pass cleanliness for the next cargo or to upgrade the tank’s surface condition.
